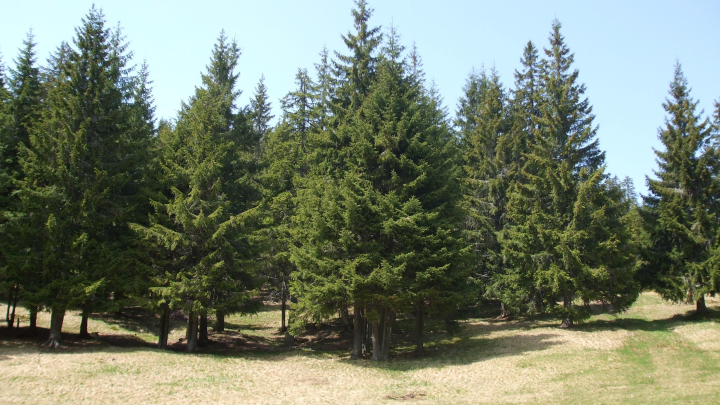
Pellets are small cylindrical fuel particles produced by compressing fine wood shavings and waste under high pressure. Wood pellets are frequently preferred in modern heating systems because they burn cleanly and are easy to transport and store. Compared to fossil fuels like coal, pellets are more environmentally friendly and offer high efficiency (with combustion efficiency ranging from approximately 85% to 95%). The type of wood used determines the quality of the pellet: the heating value, combustion duration, ash content, and mechanical durability of a pellet directly depend on its raw material. For this reason, trees such as oak, beech, pine, spruce, and poplar are often preferred, and the differences among them become significant. In the sections below, we will examine the characteristics of common tree species, their effects on pellet efficiency, and comparisons of their quality.
Most Preferred Tree Species in Pellet Production
In Turkey and around the world, the most commonly used species in pellet production are generally oak, beech, pine, spruce, and poplar. Each species has different physical properties and energy content:
Oak (Quercus spp.): Classified as a hardwood, oak is extremely dense and durable. Oak pellets offer a high calorific value per unit mass; they typically contain around 18–19 MJ/kg of energy. This is due to the dense wood texture of oak and its high carbon-lignin ratio. Oak pellets provide high heat for a long duration and burn slowly, which is advantageous for long-term heating. However, because oak wood is hard, it requires more energy to grind and compress in the pellet machine. The ash content of oak pellets (residual ash after combustion) is generally around 2–3%.
Beech (Fagus orientalis): Another hard and dense tree, beech has a high calorific value. Like oak, beech pellets are made from strong woods; their calorific value is similarly around 18 MJ/kg. Since beech trees are abundant in Turkey, they are preferred as raw material for pellets. Due to its dense structure, beech pellets provide stable combustion. However, the pelleting process can be nearly as challenging as with oak and requires high temperature and pressure. Beech pellets also generally leave little ash and produce a stable flame.
Pine (Pinus spp.): Pine species (such as black pine, red pine) are needle-leaved softwoods and are very common in pellet production. Pine pellets have lower density and a slightly lower calorific value than beech/oak pellets (approximately 16–17 MJ/kg). However, pine wood has a high resin content. This resin acts as a natural binder when the pellet is compressed and gives the pellet strength. Pine pellets generally have low ash content (between 0.5% and 1%) and ignite quickly. They produce a bright flame during combustion. Pine wood is easily ground and is widely available, which lowers the cost. Since its density is lower than beech, the volumetric energy content (energy in the same volume of wood mass) of pine pellets is relatively lower than beech pellets.
Spruce (Picea spp.): Spruce is also a needle-leaved softwood and is especially common in cold climates (such as the Black Sea and Eastern Anatolia forests). Spruce pellets have similar properties to pine. Their calorific value ranges between 16–18 MJ/kg. Spruce wood is not very resinous but burns relatively quickly and cleanly. Because it is not very dense, it is easy to pelletize. Its combustion performance is generally comparable to pine, and it is preferred due to its low sawdust smell and low ash content. Spruce pellets can be stored for a long time if kept at the right moisture level.
Poplar (Populus spp.): Poplar is a fast-growing, broad-leaved tree. Its wood structure is softer compared to hardwoods and has lower density. Therefore, poplar pellets contain less energy per unit mass (approximately 16–18 MJ/kg). On the other hand, poplar trees grow quickly, making them a sustainable source of raw material. Poplar wood is easily ground, making it suitable for pellet machines. Although its energy efficiency is lower than that of hardwoods, poplar pellets are inexpensive and abundant, reducing heating costs. Their quick ignition and rapid burning make them advantageous, especially in systems requiring short-term heating. However, due to their low density, more fuel may be needed by volume.
Pellets produced from these tree species differ in terms of heating value, moisture content, mechanical durability, and ash amount. Pellets made from hardwoods (oak, beech) generally provide high energy and are suitable for long-term combustion. Softwoods (pine, spruce, poplar) are preferred for their low ash, easy ignition, and wide availability. Which type is more suitable depends on the purpose of use and cost-raw material conditions.
Which Tree Species Offers Higher Calorific Value?
Calorific value (or heating value) is the total heat energy released when a fuel is completely burned. For pellets, this value is expressed as the heat obtained from the complete combustion of 1 kg of pellet (usually in kJ or kcal). The higher the calorific value, the more energy is released per unit weight of the pellet. Fuels with high calorific value are considered more efficient; you can produce more heat with the same amount of fuel. Therefore, the type of wood from which the pellet is made is important.
Pellets from Hardwoods: Hardwoods such as oak, beech, and maple generally have higher calorific values. For example, oak pellets have a lower calorific value of approximately 16.5 MJ/kg (about 3950 kcal/kg) and an upper calorific value of around 18–19 MJ/kg. This high energy value is due to the dense wood structure of hardwoods and their high carbon/lignin content. These types of pellets provide long burning durations and high heat per unit weight. Hardwood pellets generally have a calorific value several points higher than that of softwood pellets.
Pellets from Softwoods: Pellets from needle-leaved softwoods such as pine, spruce, and fir typically contain slightly less energy than those from hardwoods. For instance, pine pellets have an upper calorific value of approximately 17–18 MJ/kg. Since softwoods like pine and spruce have lower density and different water and resin content, they provide slightly less heat compared to hardwoods. However, the difference is generally not large, and high-quality pine pellets can achieve sufficient heating performance.
Another important point is the moisture content of the wood. In moist wood fuel, some of the energy goes into evaporating the water inside instead of generating heat, so low-moisture fuel provides higher net energy. High-quality pellets generally have a moisture content below 10%. Under this condition, hardwoods with high carbon and lignin content provide the highest calorific value when dry. In summary, the highest energy efficiency is usually seen in hardwood pellets like oak and beech; pine and other softwood pellets provide slightly less energy.
Density and Moisture Content: Tree Characteristics Affecting Pellet Quality
One of the most important factors determining pellet quality is the physical properties of the wood used as raw material. Among these, density, moisture content, and resin-lignin content stand out. Each feature affects the energy content, durability, and combustion performance of the pellet.
Density: The density of wood refers to the mass per unit volume. Dense woods (such as oak and beech) store more mass and thus more energy within the pellet when compressed. In other words, a dense pellet contains more fuel mass than a light wood pellet in the same volume. Therefore, high-density pellets are advantageous, especially in terms of storage and transport. However, very dense woods can be harder to process: strong and hard woods require more energy to grind in the pellet machine. Woods with low density (like poplar) are easier to press but contain less energy in the same volume.
Moisture Content: As the water content in fuel increases, combustion efficiency decreases. Some of the heat energy in a high-moisture pellet is spent evaporating the water in the pellet, reducing the effective heating value of the fuel and hindering efficient heating. Also, moist fuel ignites more slowly and poses a risk of mold or fungus formation in storage. In quality pellet production, the raw material’s moisture content is generally reduced to below 10%. This low moisture allows the pellet to burn for a long time and provide high thermal efficiency. In summary, the lower the moisture of the tree used as pellet raw material, the more "efficient" the fuel burns.
Resin and Lignin Content: Natural resins and lignin in the wood act as adhesives in pellet production. Resin levels are high in needle-leaved trees (such as pine, spruce, and fir). These resins soften under pressure during pelleting and bind particles together, increasing the mechanical strength of the pellet. As a result, pellets obtained from resin-rich trees are stronger and more resistant to breakage. Lignin, a component that also acts as a glue in wood cells, softens with pressure and heat and shows a binding effect in the pellet. Lignin content is generally high in hardwoods, but the resin in needle-leaved trees further enhances the adhesive quality of the pellet. Therefore, resinous wood pellets are both easy to compress and provide extra heating value during combustion (due to the oily compounds in the resin).
Ash content also affects fuel quality; trees with high mineral content leave more ash when burned. In general, needle-leaved trees have low ash content, while trunk woods such as oak may have slightly higher ash levels. In conclusion, to improve pellet quality, dense, low-moisture, and high resin/lignin content woods are preferred.
Softwood or Hardwood? Which Type Is More Advantageous?
In pellet production, tree species are generally evaluated in two main groups: hardwoods (broadleaf deciduous) and softwoods (needle-leaved). Each type has its own advantages and disadvantages:
Pellets from Softwoods (Pine, Spruce, Fir, etc.): Softwoods are usually rich in resin and have long fibers. Thanks to these properties, they act as natural binders during pellet production. The greatest advantage of pine and spruce pellets is their low ash and low ash formation; the amount of ash left after combustion is generally below 1%. Additionally, needle-leaved woods ignite quickly and start burning in a short time before delivering intense heat. This ensures continuous and clean combustion, especially in modern pellet stoves. From a production perspective, the wood of softwood trees is easier to break and grind, which requires less energy. Therefore, softwood pellets are generally more cost-effective and offer consistent quality. However, as a disadvantage, they provide an average level of energy without producing very high heat at once; meaning the temperature is slightly lower and drops relatively quickly. Also, resinous pellets may cause excessive soot and resin residue in the combustion chamber, especially in systems operating at low temperatures.
Pellets from Hardwoods (Oak, Beech, Maple, etc.): Hardwood pellets have higher density and energy content. Therefore, their burning duration is longer and they provide high heat for an extended period in the form of embers. Hardwood pellets, such as oak pellets, can produce significant amounts of heat due to their high carbon content. These types of pellets are advantageous especially in industrial boilers or large pellet heaters where long-term heat supply is required. The disadvantage is that due to their high density and hardness, the production process consumes more energy: a pellet press needs more power to grind oak sawdust, and machine gears may wear out faster. Also, the ash content of hardwood pellets may be slightly higher (around 2–3%), which may require more frequent chimney cleaning. However, in general, due to their high calorific value and strong pellet structure, hardwoods are attractive for users seeking efficient combustion.
Summary According to Usage Areas: In home-type pellet stoves, if clean combustion and low ash are a priority, high-quality pine-poplar blend pellets are preferred. That is, if maximum heat is desired in short periods rather than continuous refueling, softwood pellets are ideal. In contrast, in industrial boilers or systems requiring long-term fuel supply, hardwood pellets may be preferred because energy efficiency (MJ/kg) is the primary concern in such systems. In practice, however, many pellet manufacturers mix species and use softwoods to improve machine efficiency. Therefore, the “more advantageous” choice depends on the user’s priorities.
Sustainable Tree Species in Raw Material Supply
Sustainability is becoming an increasingly important issue in pellet production. When selecting raw materials, it is important to turn to continuous and renewable sources. At this point, various strategies stand out: Forest and Industrial Waste: The first option to protect existing forest resources is to use waste such as sawdust, fine chips, and wood scrap mixtures that emerge from sawmills, furniture workshops, and wood processing facilities. Since these wastes are already formed as by-products, their use meets most standards and also prevents unnecessary tree felling. Thin branches and pruning residues obtained from forests can also be evaluated as pellet raw material. In this way, the amount of new trees needed is reduced. For example, the fine sawdust and bark that emerge after logs are processed into lumber can be used as raw material for pellet production.
Fast-Growing Native Species: Fast-growing trees are important for sustainable raw material. In Turkey, poplar (known internationally as Populus) stands out in particular. Poplar is a short-rotation species that can yield wood in just a few years. In addition, some needle-leaved species (such as red pine, black pine) or fast-growing trees like acacia are cultivated in private gardens or plantations. When using native species like poplar, instead of exploiting natural forests, a field-style tree planting system is adopted. These trees are suitable for regular harvesting in energy forests (forests planted for energy production). Thus, raw material supply gains continuity, and the forest ecosystem remains balanced.
Local Ecosystem and Forest Management: Certified forest products are also important for sustainability. Forest certification systems such as FSC or PEFC encourage conscious management where a new tree is planted for every tree cut, and forest biodiversity is preserved. Similar programs also exist in Turkey. When waste from local forests is used, considering these types of certifications enhances environmental sustainability. Additionally, cleaning cuts performed to rid forest land of problems such as fire, pests, or disease can also provide raw material for pellet production.
Alternative Biomass Sources: In addition to wood waste, other biomass sources such as olive pomace, agricultural residues, or hazelnut shells can also be evaluated in pellet production. However, since the question specifically asks about tree species, we focused on wood-based raw materials. Still, it is worth mentioning that materials such as branch waste emerging after olive harvests can also be converted into energy pellets with suitable technologies.
The raw materials obtained through these methods are advantageous in terms of the circular economy. These approaches that enable continuous production reduce costs and protect forest health. In summary, in pellet raw material supply, the use of local, fast-renewing species and waste materials should be prioritized.
Blend Pellets: Can Different Tree Species Be Used Together?
Pellet manufacturers sometimes produce pellets by mixing more than one tree species. There are some advantages and points to consider when using blend pellets:
Advantages: Mixing different trees can improve the overall properties of the pellet. For example, when a resin-rich softwood (pine, spruce) is combined with a high-density hardwood (beech, oak), the pellet gains durability on one hand and a high calorific value on the other. Thus, the pellet can acquire both a strong and high-energy quality. At the same time, quality fluctuations that may occur due to raw material variability are balanced. It also provides cost flexibility; for example, instead of always using expensive hardwoods, a mixed product can be produced with cheap waste sawdust. As a result, both production efficiency increases and the fuel’s combustion performance is balanced.
Points to Consider: Some technical issues must be considered when mixing different species. In blended pellet production, the moisture content and grinding level of the raw material should be as uniform as possible; otherwise, compression in the pellet machine becomes inconsistent, and the breakage rate increases. In addition, certain tree species’ resin or pollen characteristics may cause different chemical reactions during combustion. For example, a certain amount of resinous pine may require chimney cleaning in systems operating at low temperatures. If the mixture contains too many different species, predicting the pellet’s combustion characteristics becomes difficult. Therefore, blending ratios are usually adjusted based on experience and test results.
Application Examples: In practice, most pellet factories process large volumes of various wood wastes in mixed form. For example, furniture workshop sawdust can be mixed with wood chips to produce pellets. Some pellet products are labeled as “mixed wood” or “soft-hardwood blend.” To achieve a durable fuel, usually a mixture containing about 30–50% hardwood is preferred. What is important for users is this: Just as 100% single-species pellets provide high efficiency, mixed wood pellets can also do so, provided that quality control is properly managed during the production process. In conclusion, using different tree species together is possible and can be advantageous. However, for consistent quality, raw material selection, blending ratios, and production processes must be carefully managed. For general consumers, mixed wood pellets are usually a sensible choice because they offer both economical pricing and strong combustion performance.