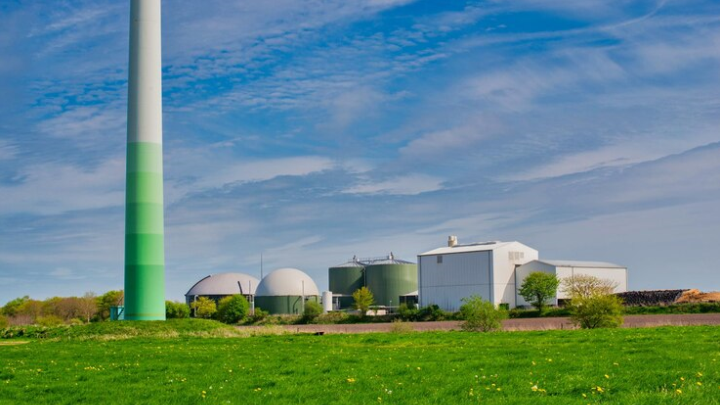
The Role and Increasing Importance of Pellet Fuel in Industrial Processes
As industrial sectors seek sustainable and cost-effective solutions to meet their growing energy demands, pellet fuel has emerged as a prominent option. Pellets made from wood, agricultural waste, and biomass are highly suitable for industrial use due to their low emission values, high energy density, and sustainable raw materials. Their standardized form facilitates logistics processes and provides high efficiency in systems compatible with automatic feeding. These features are critically important in meeting the continuous energy requirements in industrial production.
Pellet systems are particularly preferred in processes requiring consistent heat. This is due to the pellet’s ability to support controlled and steady temperature production. Pellet fuel operates with high efficiency in many areas such as furnaces, dryers, steam boilers, and thermal processing equipment. Additionally, the low amount of ash produced during combustion reduces maintenance times and minimizes production interruptions. When used as an alternative to fossil fuels, pellet fuel significantly reduces both operational costs and carbon footprints, enabling industrial facilities to fulfill their environmental responsibilities.
With the strengthening of renewable energy transition policies, public incentives and carbon tax regulations have accelerated the shift of industries towards biofuels like pellets. In the long term, pellet-fueled systems provide more predictable energy costs and offer independence in raw material supply chains. At the same time, they encourage the utilization of domestic resources, reducing external dependency and contributing to national energy security.
When applied on an industrial scale, pellet systems improve not only energy production but also production efficiency and facility management. Modern pellet boilers, which can integrate with digital monitoring systems, offer advantages such as real-time data tracking and automatic modulation. In this way, energy management becomes more effective, and resource usage is optimized. In this context, pellet fuel is not only an alternative but also a smart energy solution for the industrial world.
Use of Pellet Systems and Energy Auditing in the Food Industry
The food industry is extremely meticulous in selecting energy sources due to the sensitivity of the production process and hygiene requirements. In many processes such as baking, steam cooking, sterilization, drying, and pasteurization, the heat source plays a critical role. At this point, pellet boilers provide a clean, economical, and sustainable heating solution that can be integrated into food production processes. Pellet-fueled steam generators ensure the constant temperature needed during production, standardizing product quality. While heat fluctuations in traditional fuel systems can have undesirable effects on products, these risks are eliminated with pellet systems.
Moreover, thanks to modern automation technologies used in pellet systems, energy usage on the production line can be monitored and controlled in real time. This allows businesses to optimize energy efficiency and provides an advantage in complying with energy management standards such as ISO 50001. Another important aspect is environmental compatibility. Unlike fossil fuels, pellet fuels produce low emissions. This greatly facilitates the process of obtaining environmental permits and complying with exhaust gas emission standards for food production facilities. Furthermore, pellets made from agricultural by-products support the reuse of waste and the implementation of circular economy principles.
In production lines integrated with pellet systems, smart sensors working in conjunction with digital energy monitoring solutions can optimize the efficiency ratio between fuel consumption and product output. This makes production processes more sustainable both economically and ecologically. Additionally, by reducing carbon emissions, companies can save on cost items such as carbon taxes and gain a competitive advantage in international certification processes.
In the food industry, energy expenses typically account for 15–30% of total production costs. For large production facilities, this can correspond to an annual energy budget of millions of lira. With pellet-fueled systems, significant cost savings can be achieved. Also, by reducing carbon emissions, companies gain a strong position both environmentally and in terms of brand reputation. In summary, the use of pellets in the food sector increases operational efficiency and supports green production goals.
Pellet-Based Heating Solutions in the Textile and Chemical Industries
The textile and chemical industries are among the leading sectors that benefit from the advantages of pellet fuel, given their high energy consumption and continuous heat requirements. Processes such as dyeing, finishing, drying, steam generation, and solvent recovery require systems that operate at consistent temperatures. Therefore, the boilers and heating systems used in these sectors clearly need a reliable and continuous energy source. Pellet-fueled systems step in at this point, ensuring energy continuity while supporting environmentally friendly approaches.
Controlled combustion of pellets minimizes temperature fluctuations, preserving quality in production processes. Due to the temperature sensitivity in chemical formulations, heat fluctuations caused by conventional fuel systems can adversely affect product quality. In this regard, pellets offer a more stable solution for the chemical sector. Additionally, the compatibility of pellet boilers with automation systems increases energy efficiency. These systems, which enable continuous monitoring and real-time intervention, prevent energy losses and production downtime.
In the textile industry, pellet systems integrated with steam boilers reduce energy costs and facilitate compliance with environmental regulations. Pellet systems also play a supportive role in helping businesses meet their carbon emission targets. Considering the increasing carbon taxes and sustainability reporting obligations in Turkey and worldwide, the environmental and economic contributions of pellet-based systems become even more apparent.
Moreover, global environmental policies such as the EU Green Deal have accelerated the transformation of energy sources by enforcing low-carbon production conditions in industry. In this context, the preference for pellet systems also increases the competitiveness of companies in export markets. The integration of pellet systems provides a positive indicator in corporate sustainability reports. Considering all these factors, the use of pellets in the textile and chemical sectors has become a strategic choice in terms of quality control, energy savings, and environmental compliance.
Dual Gains in Industry Through Energy Efficiency and Waste Heat Recovery
Pellet-fueled systems can achieve significantly higher efficiency levels not only in terms of direct energy production but also when integrated with waste heat recovery technologies. Especially in large-scale industrial facilities, reusing waste heat generated by systems is the key to energy savings. In this context, heat exchangers and heat recovery units compatible with pellet systems can provide up to a 30% additional efficiency gain.
Recovered heat can be reused in preheating, water heating, or secondary production processes. This means not only a reduction in energy bills but also a decrease in the waste heat released into the environment. In energy-intensive sectors, such integrations can reduce annual carbon emissions by thousands of tons. In addition, recovery systems increase energy independence. Facilities can reduce external dependence and create a circular energy structure within themselves.
This structure also offers significant advantages in terms of compliance with energy management system standards such as ISO 50001. In order to compete in international markets, energy efficiency is now not just a cost factor but also a matter of prestige. Waste heat recovery is one of the techniques that support this prestige. Moreover, with government support and energy efficiency incentives, these investments can pay for themselves in a short time.
Furthermore, the energy obtained from waste heat recovery can be used not only in production processes but also in heating administrative buildings. This ensures a more balanced and smart distribution of energy within the facility. These multiple advantages achieved on an industrial scale allow pellet systems to be positioned not only as energy providers but also at the heart of sustainability and cost management strategies.