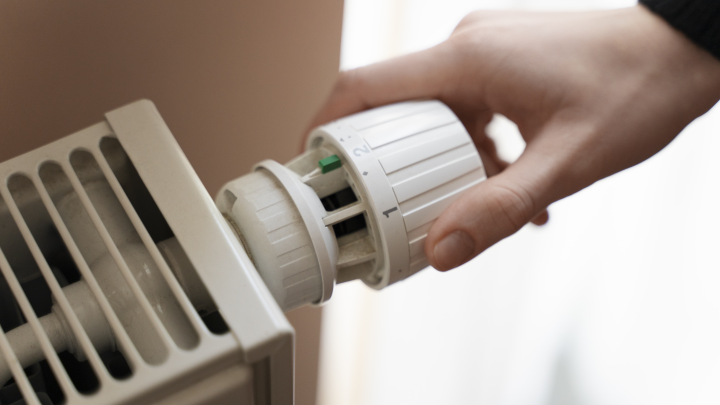
Do Pellet Users Really Pay Lower Bills?
Cost Analysis of Heating with Pellets: Comparison with Natural Gas, Coal, and Electricity
Pellet-fueled systems generally offer a lower unit energy cost compared to fossil fuels. For example, by the end of 2023 in Europe, pellet prices in bulk purchases had decreased to approximately €350–475 per ton, enabling savings of up to 30% compared to natural gas. According to a model that compares unit heat cost assuming similar energy efficiency, when the natural gas price is €1/therm, a pellet price of €160/ton is equivalent. This means that as the price of natural gas increases, savings in favor of pellets also increase. Energy organizations such as Balcas emphasize that the cost per kWh of biomass fuels can be lower than that of natural gas or oil. When compared with electric heating, the cost per kWh of pellets is significantly lower. While national averages for electricity typically hover around €0.20–0.30/kWh, pellet fuel costs around €0.07/kWh for the same unit of heat. Compared to coal, pellets are competitive under similar energy content and efficiency conditions; although coal may sometimes be cheaper, its gross calorific value is higher than that of pellets. However, when environmental taxes and nitrogen/sulfur emission costs are considered, pellets often become a more economical option. In summary, the stable price of pellet fuel and systems that can operate with high efficiency can provide savings over electricity and especially over the fluctuating natural gas prices in recent years. According to existing examples, a household using a modern pellet system may have lower annual heating costs compared to a system using electricity or fuel oil to meet a similar heat demand.
What Factors Affect Pellet Prices? Impact of Quality, Moisture Content, and Density
Pellet fuel prices vary depending on factors such as the type of raw material, the production process, the quality grade, and logistics. Pellet quality is determined especially by features defined by standards like ENplus or ISO17225 (such as moisture, ash content, calorific value, durability, and density). For example, ENplus A1 class pellets require moisture ≤10%, ash ≤0.7%, and high energy density, whereas lower class pellets have more lenient values. Generally, pellets with low moisture content, low ash content, and high unit bulk density (achieved through compression) offer higher calorific value. Moisture directly affects the thermal value of pellets: as moisture increases, energy is used to turn water into steam during combustion, which reduces the net amount of heat.
Experimental studies have shown that a moisture content above 10% in pellets increases durability but reduces combustion efficiency. Pellets with high bulk density carry more energy per unit volume.
Boiler and Stove Efficiency: How Much Fuel is Consumed with the Right System?
The efficiency of pellet-fueled systems varies depending on the type of device and the technology used. Modern well-designed pellet boilers (used in individual heating systems) generally operate with efficiency above 90%. Similarly, modern pellet stoves (fireplace or stove-type heaters that can burn wood pellets) also offer thermal efficiency between 85–90% thanks to controlled combustion and fan systems.
For example, in a house with an annual heating need of 20,000 kWh, a system operating at 90% efficiency would consume approximately 4–4.5 tons (around 4,500 kg) of pellets (based on the assumption of a calorific value of 4.8 kWh/kg). Put simply, around 220–250 kg of pellets are needed to produce 1,000 kWh of heat. Under ideal conditions—where the boiler or stove is operated at full capacity, the combustion air is correctly adjusted, and the chimney is properly designed—fuel consumption stays at this level and fuel savings are achieved. If efficiency is low (for example, if the boiler is undersized for the need or the system is not operated at optimal capacity), consumption increases. The calorific value of the pellet used combined with device efficiency determines final consumption.
Hidden Factors Affecting Bills: Storage, Moisture, and User Errors
There are various indirect factors in pellet fuel systems that do not directly reflect on costs. First of all, storage conditions are of great importance: pellets stored in humid environments absorb moisture, reducing their thermal value; moist pellets provide less net energy per unit weight. High humidity causes the pellets to swell and burn less efficiently. In addition, torn packaging or broken pellets can turn into dust, disrupting fuel flow; broken pellets absorb moisture faster and burn less efficiently. Regarding usage errors, incorrect fuel selection and usage methods pose problems: using low-quality or moist pellets prevents complete combustion and leads to inefficient fuel use.
Excessive fuel feeding settings (e.g., feeding more than needed in a fireplace) or insufficient air flow adjustment also impair combustion quality. If periodic maintenance and cleaning are neglected, ash accumulates inside the device; ashes accumulating in the combustion chamber and heat exchanger block heat transfer and reduce boiler efficiency. In addition, clogging in the chimney and feeding system causes hidden heat losses. In summary, storing pellets in dry conditions and using them with appropriate equipment depend on user training and using the right system. When these factors are considered, between two systems that consume similar amounts of fuel, the one operated more properly will result in lower bills.
How to Increase Efficiency While Heating with Pellets?
Why Might Your Pellet Heating System Not Be Operating Efficiently?
If a pellet fuel system is not operating at sufficient efficiency, the first things to check are system sizing and fuel compatibility. For example, if the boiler or stove is not selected with a capacity sufficient to meet the heating needs of the house, the device’s optimal operating point cannot be achieved.
No matter how efficient a device is, if it is incorrectly sized, it cannot fully meet the heating requirement. Additionally, device installation and chimney design affect efficiency; in cases where proper draft cannot be achieved, combustion becomes weak. One reason for poor combustion quality is disruption in the combustion pattern. Using low-quality pellets or moist raw material, incorrect adjustment of combustion air, and malfunctions in the ignition system prevent full combustion. For instance, using unsuitable agricultural pellets in a fireplace, according to Pellet Quality Standards, may result in fine ash buildup and hinder complete combustion. Therefore, combustion efficiency depends not only on the design of the device but also on the type of fuel and operating conditions. In summary, selecting a device that suits the heat load, calculating annual heating demand, and checking fuel compatibility can prevent most efficiency problems.
What Are Common User Errors Affecting Combustion Efficiency?
User-related errors have a direct impact on efficiency. The most frequently encountered mistakes include using incorrect fuel and choosing low-quality pellets. Using organic waste pellets (for example, straw pellets with high ash content) in unsuitable devices or burning pellets that have absorbed moisture during storage lowers combustion efficiency.
Moreover, if the balance between fuel feed rate and air flow is not established correctly in stove/fireplace settings, combustion gases may escape and the heating process becomes inefficient. For example, if the feed rate is set too high, the flame grows uncontrollably, increasing incomplete combustion; on the contrary, if the setting is too low, a small flame may produce smoke and carbon residues. Improper adjustment of the fan and damper settings by the user is also among the factors that reduce efficiency. In addition, improper steps in cleaning the combustion chamber lead to efficiency loss. If the combustion chamber is cleaned too early—before the fuel is fully burned—the remaining heat potential is not properly utilized. On the other hand, aggressively cleaning the device before it has cooled after ashing may cause excessive cooling of components and result in fuel savings loss during re-ignition.
How Do Ash and Soot Accumulation in the Combustion Chamber Affect Efficiency?
Ash, soot, or slag that accumulates in the combustion chamber and heat exchanger negatively impacts heat transfer. Under ideal combustion conditions, pellets are fully consumed and leave behind fine ash; however, due to poor fuel quality or adjustment issues, clumpy ash and slag may form and melt at high temperatures, sticking to the heat exchanger. This layer of residue insulates the heat exchange surfaces, causing the stove or boiler to waste a significant amount of generated heat through the chimney. This technically reduces the system’s efficiency; according to JL Phillips, in boilers that are not regularly serviced, combustion residues accumulate and obstruct heat distribution, leading to a drop in efficiency.
In addition, high-ash pellets accelerate chimney pollution in systems without filters. Therefore, pellets with low ash content should be preferred during fuel selection, and coarse ash formed after combustion should be cleaned in a timely manner to prevent the formation of surface deposits. Regular chimney cleaning as recommended in user manuals also helps reduce efficiency loss. Burning low-quality wood or agricultural pellets results in layered ash buildup, which both reduces efficiency and increases emissions. For this reason, using only ENplus or similarly quality-certified pellets and not neglecting device maintenance are critical to preserving efficiency.
User Habits: Overfeeding, Early Cleaning, and Incorrect Settings
User habits and maintenance discipline directly affect system performance. Overfeeding is a typical mistake: setting the stove to maximum in order to heat the room quickly causes excessive combustion and leads to wasted energy. A proper and controlled heat setting should be applied, and unnecessary high power usage should be avoided. In the category of incorrect settings, mismatches in parameters such as feed motor speed and air intake damper are included. If the ideal oxygen-to-air ratio for pellet combustion cannot be maintained, smoke production increases and efficiency decreases. Additionally, the timing of cleaning is also important: cleaning the combustion chamber before the fuel is fully consumed prevents the accumulated heat from being properly transferred to the system. Therefore, most manufacturers recommend leaving a certain level of ash bed. On the other hand, devices that are not cleaned for long periods lose efficiency. Sources indicate that pellet stoves require monthly cleaning, while systems like boilers require weekly/monthly maintenance.
How Often Should System Cleaning Be Done? Its Contribution to Performance
Regular maintenance is essential to maintain efficiency in pellet-fueled systems. Experts recommend monthly cleaning (emptying the ash tray, cleaning the glass, and sweeping the combustion chamber) for pellet stoves; this allows the stove to operate at maximum efficiency. In pellet boilers, internal cleaning is preferably done weekly (removal of ash, brushing the heat exchanger). Especially in systems without automatic cleaning features, manual removal of ash after each operation should be considered. One important practice during cleaning is to leave a small amount of hot ash bed after each burn cycle; this facilitates easier ignition in the next cycle and saves energy. Additionally, at least once a year, a technical inspection by a qualified technician should be performed: during this comprehensive service, the combustion chamber, fans, and nozzles are cleaned, and worn-out parts (e.g., feed motor bearings, gaskets) are replaced. Calculations in the literature also support this: if regular cleaning and servicing are neglected, soot layers accumulate in the flue and heat exchanger, significantly reducing efficiency. Therefore, by maintaining a monthly/yearly maintenance routine, the full energy of the fuel can be converted into heat, maximizing savings.
Can Agricultural Waste Be Converted into Pellets? What Is Its Contribution to the Circular Economy?
What Is Agricultural Waste? How Is It Utilized in Pellet Production?
Agricultural waste consists of organic materials left over from agricultural and food production processes. These can include crop residues such as straw left in the field after harvesting, cotton or tobacco stalks, sunflower or rice husks, grape pomace, olive pits, and similar materials. These wastes are rich in fibrous carbon and serve as raw materials for pellet production, contributing to circular economy goals. According to research, aside from wood by-products, agricultural and forestry residues such as cocoa husk, cane bagasse, corn stalks and cobs, palm fiber, wheat/rice straws, olive pits, and nut shells can be converted into pellet fuel. In the pellet production process, these wastes are first dried and crushed; then they are extruded under high pressure into cylindrical pellet form. Through this method, organic matter that would otherwise decay unused is converted into energy. Thus, waste is both recovered and fossil fuel dependence is reduced.
Which Agricultural Wastes Are Suitable for Pellet Production?
In practice, many types of agricultural residues are suitable for pelletizing. The most common examples include cereal straws such as wheat, barley, and rice straw, as well as corn stalks and cobs. Additionally, cotton stalks, sunflower and flax residues, olive and almond shells can also be converted into pellets. Sugarcane bagasse is especially used as pellet fuel in industrial production facilities. Other suitable raw materials include fruit pomace (such as grape pulp), cocoa and hazelnut shells, and walnut remnants. In summary, any agricultural waste that is rich in cellulose, has a fibrous structure, and is sufficiently low in moisture can be a potential source for pellet production. However, depending on the plant type, lignin content and structural requirements vary, so different wastes must be pressed under different processing conditions. For example, pellets made from straw have relatively low lignin content; therefore, moisture control and possibly the addition of a binder (such as a small amount of wood sawdust) are necessary before pelletizing.
What Are the Characteristics of Pellets Produced from Agricultural Waste?
Pellets of agricultural origin show significant differences from wood pellets. In general, their specific energy content (calorific value) is slightly lower than that of wood pellets. For example, the lower heating value of wheat straw pellets is around ~16 MJ/kg, while wood pellets reach ~20 MJ/kg. Depending on the raw material, ash content is also higher: cereal straws leave 4–7% ash, whereas wood pellets typically contain around 1% ash. This makes agricultural pellets a fuel that requires more frequent cleaning and solid waste management after combustion. Additionally, the bulk density of agricultural pellets is lower compared to wood pellets, which reflects in transport and storage volume. Mechanically, they may also be more fragile than wood pellets; because lignin in wood ensures strong binding, while in grasses and cereals, the lower lignin content results in particles dispersing more easily. The final product's moisture content should again be kept around 10%; when ideal moisture is ≤8–10%, combustion performance is optimal. Pellets containing high levels of minerals (such as silicon, potassium, etc.) may produce reactive ash (lime-forming substances); this should be considered in designing ash handling systems (e.g., electrostatic filters, cyclones).
What Are the Differences Between Agricultural Pellets and Woody Pellets?
The main differences between agricultural and woody pellets relate to composition, energy, and ash content. Wood pellets, with their high cellulose/lignin structure, offer high energy and low ash levels; for example, tested tree bark pellets may contain around 3.7% ash, while wheat straw pellets can reach values such as 6.7%. Therefore, the calorific value of wood pellets is approximately ~20 MJ/kg, whereas agricultural pellets fall within the ~16–18 MJ/kg range. Mechanically, wood pellets are harder and more durable, whereas straw or grass-based pellets are more brittle. The difference in ash formation after combustion is also significant; cereal-based pellets generate more ash both by volume and by weight. Moreover, some agricultural pellets may produce high-alkaline (lime and silica-containing) ash.
In Which Areas Are Agricultural Pellets Commonly Used?
Agricultural-origin pellets are typically used in large-scale energy applications. The most common areas include industrial facilities, commercial boiler rooms, and biomass power plants. For example, cereal straw or corn stalk pellets can be utilized as fuel in agricultural regions for hazelnut drying, ceramic kilns, or steam boilers used in the pharmaceutical industry. Some large boiler manufacturers offer special combustion units with rotor-based combustion zones that allow burning of high-ash pellets. These systems can operate with straw and straw-like pellets; some even switch to condensing mode to recover heat from flue gases. On the other hand, in small-scale residential pellet stoves, agricultural pellets are rarely used, as their higher ash and ash-accumulation characteristics make them unsuitable (most home stoves are designed specifically for burning wood pellets). Another area where agricultural pellets are used is in combined heat and power (CHP) plants aimed at electricity generation. Additionally, entrepreneurial agricultural pellet cooperatives and biomass plants that supply fuel to large steam boilers convert agricultural waste into economic energy resources, thus contributing to the circular economy.